The Pursuit to Replace Hydraulics - Part 2
Although a tried and trusted technology for centuries, hydraulic systems are now giving way to their key rivals, pneumatic and electric systems. Both are worthy successors to hydraulic systems, as long as you understand their strengths, limitations, and ideal applications—which we’ll now explore.
Pneumatics
Pneumatic and hydraulic systems share similar components, such as compressor, pipes, and cylinders, but a significant difference is the pressure under which air operates: just 60–120 p.s.i., compared to 1000+ p.s.i. with oil. Pneumatic compressors cannot easily achieve high pressure—they are not designed to.
The lower pressure means pneumatic systems offer reduced power density compared with hydraulics; external linkages are necessary if you want to add power. “An external linkage solution can also enhance controllability,” adds Leighton Foster, Design Engineer at Facteon.
In addition, the high compressibility of air, compared with oil, means that air is more “springy,” offering less precision. To counter this requires the addition of external mechanical stops.
Air does have benefits, though. One advantage of its compressibility is that a pneumatic actuator absorbs shocks far better than a hydraulic ram, reducing risk of mechanical damage. Air also moves more rapidly than oil, so higher speed and agility can be achieved.
Pneumatic compressors, though noisy, can be placed away in isolation, whereas hydraulic power units need to be located near the machinery, and so the noise is more intrusive. An air system also makes for a cleaner and “greener” workplace, given that there is no pressurized oil going around. Air systems do not run so hot (hydraulics require heat-exchangers to cool them), so they are safer for the workforce. Pneumatics are ideal for “clean” sectors, such as biotech, food preparation, dentistry, and pharmaceuticals.
A pneumatic system can be costly to install due to the need for external controls and linkages; also, because of its lower power density, you cannot expect to replace your hydraulic system on a 1:1 basis. However, on balance, it is still more affordable, partly because its moving parts do not need to be engineered to such high tolerances. “We’re finding that, even with the added mechanical complexity required to achieve the same power output, pneumatics are often more affordable than hydraulics,” says Leighton.
Electrics
One fundamental advantage of an electrical actuator system over its main rivals is that it uses electricity only when it is operating—which might sound obvious until you consider that hydraulic systems, in particular, require a full-time compressor, plus cooling devices and more . . . even when nothing is moving.
An electric system is cleaner, quieter, and safer than hydraulics, and much simpler to install. And while the initial investment is high, the operating and maintenance costs are lower. Electric actuators require no valves, pumps, pipes, or filters, and there is no high-pressure fluid at risk of causing leaks or injury. Electric actuator systems are used in self-drive autos, food preparation, packaging, and robotics.
What is involved in an electric system? Your main options for actuators are a direct drive using a servo motor or servo via a gearbox and screw drive. Movement comes via a linear actuator. Inside it is a screw drive (based either on ball bearings or threaded rollers), which converts rotary action into linear motion. Balls and rollers each have their plus points.
Though it offers lower tolerance, performance, and longevity, the ball mechanism is more affordable, mechanically efficient, and well suited to high-speed product transfer between stations in an automated production line.
Rollers make greater contact with the screw, so they can handle higher loads. The ability of a roller to resist backdriving can, for instance, help prevent a suspended load dropping. Roller screws are widely used in automated manufacturing systems, particularly in forming and piercing presses.
An electric actuator is fully programmable, giving precise control over position, power, and speed. What really sets an electric system apart, however, is that it is an ideal fit for smart manufacturing, and we will unpack this in the next instalment.
Guidance is key
With decades of experience in tailoring automation systems to client needs, the team at Facteon can audit your setup, review your goals, and then discuss the design options you have to advance the efficiency of your manufacturing line.
Find out more
Speak with one of our consultants to find out about the alternatives to hydraulics for your factory automation solutions. Contact Facteon via our contact page.
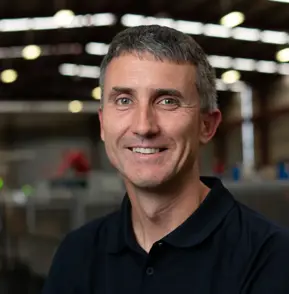
Mark Elder
Leighton Foster
Having started his career at Facteon as an apprentice, followed by working as a tradesman in the machine shop & assembly/commissioning team, Leighton has vast knowledge and understanding from the design and practical side of building and commissioning machines. Now as a full time Design Engineer Leighton brings valuable insights and experience with real-life behaviors of pneumatics vs hydraulics vs servo on machinery.