The Pursuit to Replace Hydraulics - Part 1
Hydraulic systems in one form or another have powered factories for centuries. They deliver high power with a decent measure of control. But for all sorts of reasons, customers are beginning to turn to alternatives. Let’s take a look at the ups and downs of hydraulics.
Productivity a bonus
On the plus side, hydraulics can deliver very high tonnage, thanks to the fact that oil is essentially incompressible, so whatever’s displaced is put to work. This makes hydraulics ideal, for instance, for a powerful press or a notching machine. Oil’s incompressibility means, too, that you get a good measure of accuracy and repeatability: using flow control, you know where a ram is going to stop every time. And excluding the power pack, hydraulics delivers high power density—so you can realize more power per volume and achieve greater efficiency and productivity.
In certain situations, however servo hydraulics are no faster than electric servo transfer – and we have found electric servo systems easier to tune than servo hydraulics. Also with no digital feedback available in a hydraulic system, it’s hard to keep precise track of performance or predict problems. (Addition sensing can be added, but at a cost.)
Cost
Hydraulic systems are expensive to install. When we put hydraulics in, we need to call on specialist engineers to specify power packs, pump sizes, safety valves, and pipes. We also need them to commission the line. Installing pipework is costly, and it’s hard work getting flexible pipes to look tidy. (Also, hydraulic specialists are becoming fewer in number, and this skills shortage means that customers are increasingly turning away from hydraulics—which in turn means fewer specialists . . . and so on.)
For a number of reasons, hydraulic systems are costly to run and maintain. For instance:
- The oil runs hot during use and must be kept within the optimum working temperature band by using fans or chilled water systems—which means adding extra cost, energy demands and inefficiencies. (If the ambient temperature of your workplace is particularly warm or cold, this will exacerbate the problem.)
- Hydraulics need dependable system pressure and volumetric flow. To sustain these, the electric motor that generates flow is always on, and therefore power-hungry. (All-electric systems, by contrast, mostly consume power only when you use them.)
- Servicing and troubleshooting filters, pumps, and valves requires specialist attention, as do power packs, leading to higher long-term maintenance costs. The need for high safety tolerances only pushes these costs up.
Safety and the workplace environment
Hydraulics are messy and potentially dangerous when they go wrong. A hole in a hose—even pinprick-sized—can inject oil under a worker’s skin. (Safety aside, a big burst can lead to oil spraying everywhere, which takes hours to clean up.)
Hydraulics tend to be noisy, too. Their power packs typically have large motors to meet the high demands of the hydraulic system, and they can easily run around 85 decibels.
Illustration of a hydraulic leak
But what about servo-hydraulics?
One option is integrating servo-hydraulic actuators in hydraulic systems. They do improve control and performance, but they are expensive to buy and hard to tune. Added to that, a servo-hydraulic system requires ultra-pure, multiple-filtered oil to meet acceptable ISO 4406 contamination criteria, which adds further cost and complexity. So, at present, they’re not the most cost-effective and efficient replacement for standard hydraulics.
So, what’s the way forward?
In our next instalment, we’ll look at the main alternatives—electric or pneumatic—and how to make the transition efficiently and cost-effectively.
Find out more
Speak with one of our consultants to find out about the alternatives to hydraulics for your factory automation solutions. Contact Facteon via our contact page.
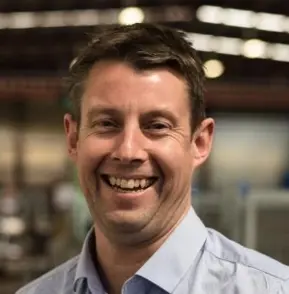
Greg Purcell
Greg’s role involves leading the implementation of Facteon’s Industrial IoT solutions for our software product, COSMOline. With his prior experience as a Facteon Control Systems Engineer, Greg brings a unique perspective and a strong understanding of PLC’s. He’s also a certified integrator of Ignition by Inductive Automation. Greg plays a key role in defining and implementing Facteon’s modern day SCADA approach that aims to prevent SCADA becoming a bottleneck for machine data.
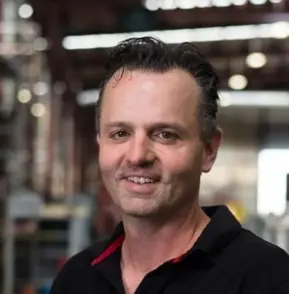
Andrew Stackpole
As General Manager of Manufacturing, Andrew is a strategic leader continuously working to ensure all project-contributing teams are in tune and in step with each other, working in an ever-increasing versatile manner across all disciplines, trades,
and pressure points within the project life-cycle. He manages the entire build process from initial assembly through to installation and commissioning, both in Facteons facilities and on customer sites.