The 20/20 on Machine Vision
What is machine vision?
The term ‘machine vision’ usually refers to computer vision in an industrial setting. Essentially, it’s the operational guidance or functioning of a device through the capture and processing of images. Applications range widely, from guiding pick-and-place robots (in packing or assembly roles) to identifying, measuring and inspecting.
In recent years, computer vision systems have grown in popularity since proving successful in track-and-trace roles within the pharmaceutical and food industries – and especially since the evolution of cloud-based computing, machine learning and AI.
What’s inside a vision system?
A typical machine vision system consists of the following elements:
- Illumination – to light the field of operation and ensure imaging quality
- Lens – to capture the image
- Sensor – to digitise the image
- Processor – to review the information using computer algorithms and make a decision
- Communications – to report the information or decision.
How many dimensions?
Vision in the industrial environment can be broken up into 1D, 2D and 3D, each with advantages in specific applications.
1D vision
A single line of pixels is analysed at a time (on the X axis). This relatively simple technology is used extensively in barcode scanners.
2D vision
The field of view is captured and analysed in two axes (X and Y). 2D vision usually features an area camera, although line-scan cameras (which read image data one pixel line at a time) can perform a similar function. 2D is widely used in measurement, inspection, machine guidance, identification of 2D codes, and OCR scanning.
3D vision
3D vision uses either two stereoscopic cameras with a structured light source or a laser line-scanner. The laser line-scanner is technically referred to as 2.5D as it requires motion in the Y axis; once the line images are assembled, the result is 3D.
Applications
In industrial scenarios, vision systems are frequently integrated into robotics and automation, and their applications fall into four main categories: guidance, identification (or traceability), gauging (or measurement), and inspection (or process control).
Guidance – for example, a 2D camera is used for pattern matching (through colour and/or shape) to identify a part’s location, alignment and orientation. Guidance systems are useful in pick-and-place robots, or in collaborating with other smart robots to process parts.
Identification / traceability – for example, a 1D or 2D camera scans an airport label or a barcode/QR code in order to collect data.
We helped a client use vision-based code readers to check laser-applied QR codes on parts at critical points in the manufacturing process, in order to ensure traceability. The collected data can be stored on a server and/or uploaded to the cloud.
Gauging / measurement – for example, a 2D camera or laser line-scanner is used to check (within milliseconds) the identity, alignment and location of a part during or after assembly, all without touching the part.
Inspection / process control – for example, a machine vision system (in place of a human) compares what’s in front of it with a databank of images. For instance, it might check a blister-pack of pills is complete, and take a pass/fail action.
We helped a client use a vision system to take multiple combined scans and inspect the quality of laser weld profiles. In our extensive experience with laser welding we have identified a direct correlation between weld strength/quality and the topology and colour of the weld. Our COSMOweld solution utilises a line-scanner (with a resolution of 1.5 µm) to create a profile of the weld at every 0.3 mm, resulting in a 3D inspection.
After stitching together multiple images of a weld, and filtering out the base material, the vision system analyses the remaining elements. The colour and immediate area are assessed against predefined criteria to gauge the weld quality.
What are some advantages of machine vision?
Machine vision can add functionality to a business operation that is moving towards automation and the future factory model. It can align your company with Industry 4.0 and the IoT, it makes robust use of cloud computing, and it sets you up to utilise AI.
At a more detailed level, it:
- has a smaller physical and economic footprint than a human equivalent;
- can enable an automated assembly line to recalibrate itself for multiple different operations;
- can ‘see’ over much a wider wavelength, e.g., into infrared or x-ray, enabling the automated vision to analyse stresses within materials;
- can collaborate with humans (for instance, after a worker performs a complex assembly, a machine checks it);
- reduces contamination / physical damage thanks to the lack of physical contact;
- can take the place of humans in hazardous environments;
- is faster, more accurate and consistent, and enables greater consistency and higher resolution, than a human equivalent;
- enables tighter process control than conventional or human equivalents;
- aids worker safety (e.g., by moderating its movements when humans are within range); and
- can reduce factory downtime by serving in a machine-tending capacity performing auto-maintenance.
Do you need a machine vision system?
Whether or not a vision system is for you, and, if so, what type, depends on a number of criteria.
Environment: Are your plant and processes sufficiently structured and ordered to make best use of automated vision and processing? (In less-structured environments, human workers are generally better.) Does your plant contain contaminants – e.g., oil, chemicals, airborne contaminants – that may interfere with vision and compromise performance?
Range: Does your work operate at a range that suits machine vision? For example, if vision sensors need to be at some distance from the assembly point, larger lenses are required.
Scale of operation: A full vision system can cost tens of thousands of dollars. It can be cost-effective in the large-scale production of relatively simple products, or – at the other end of the scale – low-volume output of complex and costly products. In other situations – for instance, an assembly-line stage requiring a single basic ‘yes/no’ decision – you could settle for a ‘simple’, rather than smart, vision sensor. The cost of set-up time and training also needs to be factored in.
Expectations: We often find that when clients who are new to automated vision systems expect them to be ‘magic bullets’, they typically turn out otherwise. Here’s where it pays to talk to a trusted consultant who knows your set-up and your pain points, and can steer your strategy. We work with a range of vision system brands. If it’s clear that machine vision will benefit you, we can help you choose the right products for your application.
Find out more
Speak with one of our team to find out whether your business will benefit from vision technology. Contact Facteon here via our contact page.
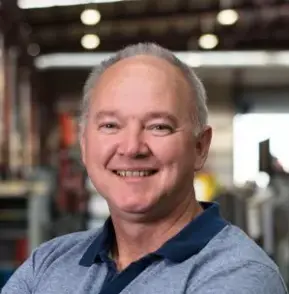
Ray Russell
Ray is a Control Systems Engineer by trade, he holds a depth of experience in avionics and automated cell integration. He is a member of Facteon's Advanced Engineering team and works across the business through the design, development and commissioning phases of custom production machinery and off-the-shelf robotics integration. He also has extensive experience and understanding of machinery safety to international ISO standards.
He also works closely with Facteon's Industrial IoT products team in the identification, development and integration of sensing technologies for data processing and analysis of machinery effectiveness, predictive maintenance and OEE.