Safety is Built In at Facteon
Gone are the days when safety was often an afterthought in the factory—a set of bolt-on measures that often reduced productivity, tempting staff to bypass them and take risks. Today, safety is designed into automation from the start, leading to fewer accidents, a more ergonomic partnership between worker and machine, and higher productivity and output.
As a customer, however, it can be overwhelming to navigate the complex world of industrial technology and ensure that your operations not only create a safe environment for your workforce, but also comply with regulations. That’s where Facteon comes in.
Safety as standard
Experts in safety, we prioritize it in everything we do and work closely with you to ensure that you are covered. You don’t even need to specify safety—we do our due diligence and cover it as a matter of course.
That doesn’t mean we shut you out. Our agile, co-creative design process ensures we work closely with you to deliver automation solutions that are tailored to your unique requirements. We’ll spot all the variables, even if they’re not initially specified, and design safety into every step.
Qualified engineers
Our best asset is our people, and we make sure they are qualified to the highest possible standards.
Three of our engineers are CMSE® (Certified Machinery Safety Expert), a globally recognized qualification issued by Pilz and TÜV NORD that guarantees a 360-degree approach to machinery safety. Retaining CMSE qualification requires a refresher every four years.
Engineers and subject matter experts Lawrence Owen and Derek Neilson also have Agile Project and Delivery Management Certification through ICAgile, which supports the application of our adaptive and collaborative design process.
Beyond qualification, we ensure your machinery is compliant in every aspect and conforms to essential standards and regulations. These include, for example, AS/NZS 4024 (safety of machinery), IEC 60204 (safety of machinery—electrical equipment), and ISO 12100:2010 (safety of machinery—general principles for design—risk assessment and risk reduction).
Over and above these qualifications, our engineers apply their knowledge and experience to implement best practice in every design.
The best solution for your needs
Our agile design process is driven by productivity, simplicity, safety, and cost. All are interrelated—so we will pursue the simplest solution to giving you safe machinery that meets both your productivity goals and budget. And we apply these principles at every step in the process, maintaining a two-way discussion with you to ensure the co-creative process delivers the best result for your needs.
As Facteon Senior Mechanical Design Engineer Lawrence Owen explains, “With any project, a risk assessment is one of the first things we do. It begins with the concept design, but we reassess throughout the project, and once the machinery is built it will be checked again by multiple people in a range of ways.”
Lawrence gives a recent example. “We were engaged to design the electrical controls for a custom pneumatic press. During this process we identified a number of safety issues, the mitigation of which were outside of our original scope of work. Had we narrowly fulfilled our contract, we would have been paid, but the customer would have been left with an unsafe and unusable press. We instead engaged with the customer, offering advice on the mechanical concept and training on risk assessment; collectively overhauling the design. The immediate result was a simpler, more ergonomic and safer press, the knock-on was a happy customer with a few extra skills in their back pocket.”
Because we consider your end goal and work backwards from there, that can mean rethinking a concept. “On one automation project, a stacker,” explains Facteon’s Automation Technical Lead Derek Neilson, “the original solution was going to be onerous, both in terms of safety as well as daily operation. So we asked, how can we achieve the desired outcome with a different design? We tackled it from a whole different angle. This meant redesigning the infeed process.”
That meant greater up-front cost, but it led to a viable safety solution, with greater productivity, ultimately providing a better return on investment and future-proofing the customer’s operation.
Find out more
Speak with one of our consultants to find out how your business can benefit from smart manufacturing. Contact Facteon via our contact page.
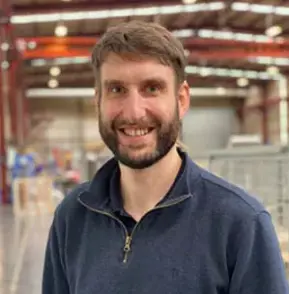
Derek Neilson
As Facteon’s Lead Automation Engineer, Derek is focused on the design, programming, commissioning, installation and support of control systems. He also works to implement data collection and manipulation. Derek is passionate about developing an in-depth understanding of the technology utilised in a manufacturer’s production line. This commitment ensures seamless integration and efficient project delivery. Derek’s work experience is backed by a Masters of Engineering specialising in Electrical and Computer Engineering.
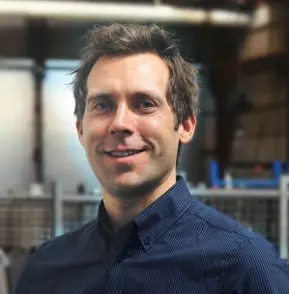
Lawrence Owen
Lawrence has a wealth of experience designing high volume production machinery for manufacturers across the globe. He’s also an experienced project manager committed to ensuring every project is delivered on-time and to specification.