Robots in automated manufacturing: should you use them?
An interesting takeaway in the article is that the price of robots has dropped relative to the cost of labor, making the direct costs of robots lower now than twenty years ago compared to labor costs over the same period. This is great news, as robots have become central to many factories’ automation transformation. From precision assembly to handling hazardous materials, robots have proven their ability to revolutionize production processes. However, robotic implementation is not universally appropriate.
This article briefly discusses considerations as to whether robots may, or may not, be appropriate for your factory.
Why robots may be ideal
Two reasons why robots are an ideal automation choice are: 1) flexibility; and 2) performing complex, repetitive, and high-volume tasks. Both points are discussed briefly below.
- Flexibility: Automation equipment has been used in factories for over eighty years. Most automation machines are built for purpose. For example, a pick-and-place machine or material transfer machinery is fixed in terms of its X, Y, and Z axis movements and have limitations set to the product and line for which it was designed. Another example is fixed welding automated machinery, which can only perform the welding tasks on the products for which it was specifically designed. This line of thinking can be expanded to other forms of automation as well.
Robots, on the other hand, are extremely flexible and can be used for material transfer in one year, and in the next year, be used for welding (or other task) by changing the end-of-arm manipulator and its programming. This flexibility means that a robot, is able to be repurposed efficiently as the needs of the factory change. - Complicated repetitive and high-volume tasks: Many repetitive and high-volume manufacturing processes can be handled by non-robotic automation such as welding, packaging, material handling, and some assembly processes. However, as robots have multiple axis (many larger robots available are six-axis robots) and have a specialized end-of-arm tooling they are capable of handling more complicated tasks that require complex material or tool manipulation. For example, robots are usually used to insert the dashboard of a car, which is heavy and must be manipulated through specific openings in the car chassis – a complicated manipulation that would be difficult to perform with non-robotic automation.
Other factors to consider
Although the above points are great reasons to choose robots over other forms of automation, robots may not necessarily be the right choice for your factory. Other factors to consider are: 1) cycle time; 2) space requirements; and 3) specialized talent requirements.
- Cycle time: Although robots can theoretically have an extremely fast cycle time, we have found that in many cases it is slower than more specialized non-robotic automation. This is especially in the case of material handling tasks, where a large heavy object is being held at the end of the robot’s arm. If the speed is too great, substantial stress on the gear box is created, which causes accelerated wear and more frequent down time reducing the Overall Equipment Efficiency (OEE). Weight of the end-of-arm tooling and any material being held at the end of the robotic arm should be accounted for when conducting any cycle time analysis.
- Space requirements: Factory floor space is invaluable and needs to be used as efficiently as possible. Safety requirements require a substantial area around the robot to be guarded as a robot moving at cycle time can easily injure or kill a person. Safety fences are the most common guarding around a robot, among other safety measures, and occupy 60+ square feet (~6+ square meters) of factory space depending on the robot's size and its reachable workspace.
- Specialized talent: Unlike non-robotic automated machinery, robots require specialized talent for maintenance, upkeep, and repair that differs from the non-robotic automation programmable logic controllers (PLC) . The programs operating robots can be extremely complex, and each brand of robot has its own coding language. If a robot has a fault and is not operating correctly, it requires specialized skills, usually specific to the brand of robot, to get the robot working correctly again. A robotics engineer on staff or available through an outsourced service provider can be quite costly and may not be available in your area. When considering robots for your factory, make sure to look at the availability of talent (directly employable or through contract outsourcing) to service and maintain them. Typically, it doesn’t make sense to hire a robotics engineer if your factory/company only has a few robots.
Conclusion
Addressing the question: “Should you use robots or non-robotic automation in your factory?” - the answer really depends. Before integrating robots into your manufacturing processes, it is important to conduct a detailed cost-benefit analysis, identify areas where the flexibility afforded by robotic automation is worth the cost related to cycle time, space, and talent requirements. In some cases, robots make absolute sense, in other situations, non-robotic automation or even no automation is better. The answer really depends on the specific needs of your factory.
If you are considering adding robotics to your manufacturing operations our team of engineers are more than happy to discuss with you the pros and cons and how they may related to your specific circumstances.
Facteon is a full-service industrial automation company capable of designing, fabricating and installing bespoke manufacturing lines or individual cells. Furthermore, our team is capable of refurbishing or upgrading your automation equipment as well. Feel free to reach out to us by contacting us directly.
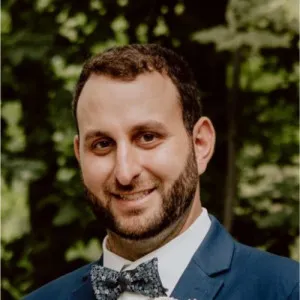