Lighthouse Factories: Lighting the Path to Manufacturing Success
Shining examples
“Lighthouses” in the manufacturing sector are factories that have implemented Fourth Industrial Revolution (Industry 4.0) technology so successfully, and evolved so effectively in scale, production, agility, and efficiency, that, like their maritime namesakes, they light the path to success, giving other manufacturers a “beacon” by which to steer.
The lighthouse concept is largely the brainchild of the Swiss-based World Economic Forum, which researched these qualities across more than a thousand manufacturers around the world, and co-published (with McKinsey & Co.) its findings in a 2019 white paper.
WEF and McKinsey have established The Lighthouse Network, a global platform for helping manufacturers identify and adopt successful Industry 4.0 strategies. As well as fostering collaboration and sharing insights, the network curates a list of factories worldwide that qualify for lighthouse status. The list numbers over 130 at present and continues to grow.
Six of these factories are run by clients of Facteon: Haier (four) and Arçelik (two). Reinaldo Silva, Facteon’s head of operational excellence, sums up how our common business goals align with those of lighthouses. “In improving existing factories, equipment and software, we set out to reduce downtime, costs, and waste (in terms of product and time), and to increase efficiency and profit.”
What makes a lighthouse?
Lighthouses are capitalizing on three mega-trends in manufacturing: connectivity, flexible automation, and intelligence, say WEF and McKinsey. They represent “the leading edge of adopting technology at scale,” and while their output may range widely, from soap powder to semiconductors, certain broad factors correlate. For instance:
- They inject human capital. Rather than focus on replacing human workers with robots, they reinvent human work, making it more varied, dynamic, rewarding, and productive.
- They reset benchmarks: these companies are not merely evolving by degree: they’re undergoing major step changes through their successful implementation of smart manufacturing. In some cases, they’re completely reconfiguring their end-to-end value chain, opening new economic opportunities for partners and suppliers.
- They’re open innovators: They are knowledgeable early adopters who share their expertise with other businesses (albeit with the necessary partnership agreements and safeguard of cybersecurity), and they collaborate for the success of the wider sector and for better, more sustainable, and scalable manufacturing environments.
- They’re diverse: some lighthouses are small to medium, for instance, and/or are based in developing economies.
Metrics of success
Lighthouses’ measure of success lies in meeting very high standards across four categories:
- They have achieved significant impact (ranging from productivity, quality, flexibility, and efficiency to improving the value chain and benefiting the community or wider industry).
- They’ve successfully implemented Industry 4.0 technologies at scale.
- They’ve performed strongly on critical enablers, such as change management, capability building, and collaboration with global Industry 4.0 communities.
Digital technology at the heart
Industry 4.0 technologies underpin the operations of lighthouses. These can include engineering, automation, robotics, automatically guided vehicles (AGVs) and intelligent materials handling systems, AI and computer vision, 5G and edge computing, all interconnected for automated analysis of day-to-day operations and identification of opportunities for optimization.
Facteon is proud to be working with large-scale manufacturing customers that were able to have many factories qualified as lighthouse factories by the WEF. The digital transformation successfully implemented across these factories not only boosts productivity, but also reduces costs and waste in all its forms.
Forward thinking
Cutting-edge tech alone, however, isn’t a magic bullet. It’s estimated that more than two-thirds of manufacturers who implement advanced technology fail to evolve beyond pilot mode. McKinsey research shows that fast action is a key prerequisite: companies that adopt AI within the first five to seven years, it calculates, can expect cumulative cashflow growth of 122%, whilst that figure for late adopters is around 10%.
Clarity of vision and purpose is also important. Enno de Boer, a senior partner at McKinsey, lists three must-haves: “First, clear strategy. Without that, you get stuck in pilot purgatory, never seeing which technologies matter for your business. Second, workforce capabilities. Without enough of the right skills, your transformation runs out of steam. Third, strong governance. Without a real execution engine, you won’t capture impact or keep improving.”
If you are at an early stage of your Industry 4.0 journey, Reinaldo Silva lists four key tips to get started:
- Try to make smart manufacturing and digital transformation initiatives a top priority in your business plan.
- Identify trusted partners with a track record on delivering both the technology and the operational know-how at scale.
- Focus on starting with small initiatives that offer shorter returns on investment; be prepared to fail fast (and learn from that), and expand gradually, prioritizing the core areas of your business that offer the highest potential for growth and profit.
- Remember that technology does nothing by itself; it’s people that make it work.
Find out more:
Speak with one of our consultants to find out how your business can benefit from smart manufacturing. Contact Facteon via our contact page.
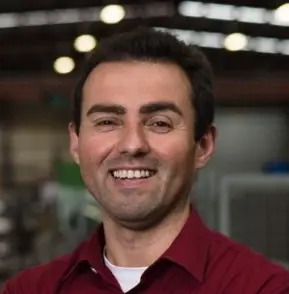
Reinaldo Silva
Reinaldo is our General Manager of Sales, and Board Director. He is currently responsible for our global sales operations and customer experience across our markets in Australasia, USA, Latin America and Europe.
His experience leading a number of different functions at Facteon over the years has provided him with a great level of understanding, and hands-on experience on what it takes to deliver great outcomes to our customers and partners.