Introducing The New Era of Robotics Teaching
*A user frame is an x, y, z coordinate system that is aligned with an object’s location and rotation. It is defined with respect to the robot’s own world coordinate system and is useful for teaching the robot points on a fixture or work piece.
Pictured: Robot and touch probe during the testing phase at Facteon's facility.
The Robotics Teaching of Yesterday
Prior to the development of this new technology, teaching a robot a user frame was a largely manual process which needed to be completed by a technician with an automation background. The commissioning stage was often slowed due to the complexities of the robot teaching process. The Facteon team identified an opportunity to revolutionise robotics teaching as it is both time consuming and vulnerable to human error.
The Modern Approach
The technology we have developed simplifies the process of teaching a robot a user frame. Rather than a human operator manually driving the robot to different points so it learns the point of origin for a user frame, a touch probe and software program are utilised to teach the robot semi-automatically.
The deployment of touch probes to analyse and record 3D surfaces of a workpiece for CNC machines is common place throughout industry. This ability to analyse a surface was built upon to develop the software used for robot teaching. The robot establishes its parameters by searching for and recording certain points on a work surface. A separate program is then run to calculate the user frame. This is a relatively simple development which has the potential to achieve significant time and cost savings during the commissioning phases.
As Facteon integrates and programmes robots on site prior to pack down and shipment to the customer’s site, it is critical to speed up the robot teaching process. As the COVID-19 pandemic simultaneously calls into question the business rational behind sending multiple experts to a customer site to manage commissioning, the need for a robotics expert on-site is also problematic. By simplifying the teaching process, manufacturers ultimately have greater certainty that their production line will be delivered on-time and to specification.
Teaching a robot manually can take over a day depending on how difficult it is to align the robot to the surface of the fixture or object and how skilled the operator is at driving the robot. With this new technology, these time-consuming factors are no longer an issue and teaching time could be cut down to less than half the original time taken.
The Role of Smart Manufacturing
The purpose of smart manufacturing technologies is to improve the efficiencies of the manufacturing process. The current method is very much dependent on the skill of the operator. The slightest movement of a work piece or station means that the robot must be re-taught. With this new technology, you would have to reteach the robot but the process of doing so is far simpler.
With AI technologies consistently adding value to the manufacturing industry, the ultimate goal is that the process will be fully automatic and the robot will teach itself the parameters of its user frame. AI has, and looks to continue, shaping the future of the manufacturing industry. Smart manufacturing technologies are making operational excellence increasingly achievable for manufacturers of all sizes. Powered by this innovation, manufacturers can now have certainty in their ability to meet market demand on time with accurate robotics solutions.
Ultimately, this technology has the potential to evolve to a customer-friendly program where an expert would not be required if the robot needed to be retaught. The customer simply needs to attach the probe to the robot and run the program. In the future, there is clear potential for this technology to be offered as an after-sales service for manufacturers.
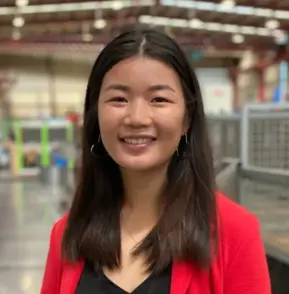
Debbie Peng
As an Engineering Intern with Facteon, Debbie is focused on automating the set up process for robotic arms through the smart application of software. Debbie is set to graduate the University of Auckland in 2021 with a Bachelors of Engineering (Honours)/Bachelors of Commerce conjoint degree, specialising in mechatronics, and majoring in marketing and finance.