How we Mitigate Risk in Automation Projects
As automation designers and fabricators, we manage and mitigate project risk at every step, from supply chain issues to technical performance and safety of operation. Anticipating risks, and designing effective responses to them, is key to keeping a customer’s project on time, on budget, and on performance, while also underpinning safety in the workplace.
Using a strategic approach, we adopt four overarching rules:
- We work with the customer to identify risks as early as possible.
- We mitigate those risks through good design and thorough planning.
- We communicate clearly and continuously with the customer on risk mitigation.
- We document and monitor risk mitigation through the entire integration process. During the concept design stage, for instance, we’ll be scanning and testing for key technical risks, planning ways to avoid them, and giving early feedback to the project team.
Risk mitigation as a strategy
Risk impact factors will be different for every project. “Therefore,” explains Jonathan Choy, Mechanical Design Engineer at Facteon, “our high-level approach to risk mitigation begins at the concept stage. Engaging early with the customer, we hold risk management meetings where we can identify suitable areas for automation, and fully understand the customer’s goals and expectations.”
We’ll use a risk matrix to keep a close watch on any high-severity, high-probability risks, to determine mitigating strategies, and to set risk thresholds. “There will always be a plan, which can be used to measure the impact of the risks,” says Jonathan. “And we may even separate the contract into stages, including proof-of-concept and experimentation, so that the customer does not need to commit to full implementation without a proven concept.”
Designing against risk
Foreseeing risks early means we get to build mitigation into our design concepts. We believe in a fail-fast attitude: where technical risk is high, we will prototype key components of the process iteratively to ensure that the concept works. “Prototyping is a critical step that will happen during the sales or design phase to validate the concept will work before we invest too much in it,” explains Jonathan.
For example:
- When developing a new product—such as a fridge door—that requires a new form, we’ll undertake trial embossing and tooling to measure the press tonnage required and thereby predict its impact on the project budget.
- In fine-tuning an assembly process, we might want to check the flatness of a wooden pallet, and how that will affect accuracy in the positioning of finished parts being palettized.
- For a robot vision application, we’ll obtain the part from the customer, then set up a range of cameras and lighting options and check them for part or pattern recognition. We measure the critical details and variables, and then choose the best camera and lighting solution.
- To test welding (including laser welding), we’ll use a full trial setup to determine the required settings. The customer supplies the materials and we can then prove whether they are weldable—down to details such as how to weld particular lengths of stock, or the duration of a weld cycle time.
Looking ahead
Identifying technical risks during the design phase enables us to create systems that can be upgraded easily to accommodate changes down the line. “A simple example,” explains Jonathan, “is our electrical cabinets, which have, by default, an allowance of 20% to account for any additional input–output requirements that might develop throughout the design and commissioning process, as well as allow for future growth.”
We take a similar approach with machine cycle times. “We estimate these based on our knowledge of past machines and, where possible, on simulation exercises. This estimate must be below the required cycle time by a range of 10–20% depending on the certainty of the application.” This enables Facteon to address a key risk: namely, a machine that will not meet its throughput requirement, which is a costly and time-consuming issue to resolve.
Registering risk
Throughout every project, Facteon uses a risk register, which enables us to judge whether to mitigate, accept, avoid or transfer each risk. For example:
- Mitigate: If there’s a risk of shipping delays, our mitigation is to communicate with the customer and identify other supply chain routes.
- Accept: When supplier cost increase is the risk.
- Avoid: Avoid shipping delays by choosing to assemble and commission on site, instead of commissioning first in New Zealand.
- Transfer: If a box palletizing process is technically uncertain, we may outsource it to a specialist company rather than develop it inhouse.
At every stage, we communicate with the customer, highlighting key risks as they arise. “Every good project manager knows about the value of open communication and a constant feedback loop,” says Jonathan. “Using an agile process, we make sure design information is shared as soon as possible, through daily stand-ups and project updates. This visibility and open collaboration ensures that we deliver future-thinking solutions for both operational and competitive advantage.”
Find out more
Speak with one of our team to find out whether your business will benefit from smart manufacturing solutions. Contact Facteon here via our contact page.
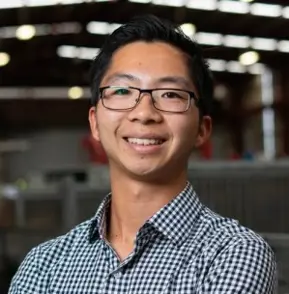
Jonathan Choy
Jonathan joined Facteon in early 2014 as an Engineering Cadet following the completion of a Bachelors of Engineering at University of Auckland. The role of Engineer Cadet involved a rotation around various business units from design through to automation and control systems. Since completing his Cadetship in 2016, Jonathan moved into the role of Design Engineer. He’s since contributed to the development of a range of flexible manufacturing systems.