Finding and Nurturing the Skilled Future Factory Worker
We noted in a previous article how the general shortage of labor is driving forward-thinking manufacturers to adopt advanced manufacturing technologies and factory automation. We’ve also seen how the pandemic rattled the global supply network, prompting many businesses to reshore or near-shore their manufacturing.
These future-facing businesses need a domestic labor force who possess “smart skills”—in fields such as robotics, automation, and data analysis—as well as a toolkit of human skills, such as adaptability and strong communication.
With the rapid pace of technological change, however, skill sets are evolving. The job scope of, for instance, an automation engineer today may be completely different in ten years’ time. The challenge to both manufacturing and the education sector is this: how do we create and sustain a pipeline of smart talent for tomorrow’s factories? And what does that talent look like?
New times, new skills, new opportunities
The cohort of baby-boomers that underpinned traditional manufacturing the past few decades is retiring, and the new-generation workers have different expectations. They’re after a good work/life balance, for instance, and a progressive approach to DEI: diversity, equity, and inclusivity. They will also use a constantly evolving repertoire of new skill sets.
A recent UK survey asked manufacturing engineers for predictions on the future profile of their role. Three-quarters of them foresaw major changes in engineering roles and skills over the next 10–20 years. As to which knowledge and skills will likely be most important to these new roles, the top five included automation, robotics, and mechatronics; artificial intelligence; digital manufacturing; and simulation and modelling. And as to which competencies will be important, the top five were non-engineering: communication skills, creativity, design thinking, team building, and change management.
This indicates that a mix of soft skills and knowledge, alongside more traditional disciplines, will be ideal. The survey noted, too, that “the pace of change of technology is increasing and engineers embarking on their careers will need to refresh their skill sets a number of times across their working lives.”
In the long run, manufacturers stand only to gain by embracing new, data-driven technology, and by nurturing and sustaining a workforce with future-facing skill sets.
With smart manufacturing, monotonous tasks are automated, so workers can look forward to greater job satisfaction as they upskill and take on more nuanced, rewarding roles. Humans and robots collaborating through connected, intelligent and flexible solutions creates an optimized workplace with happier and more productive staff.
Nurturing the skilled labor pipeline
As a World Economic Forum (WEF) report puts it, “Our responsibility is not to protect the jobs that machines can do better, but to prepare the labor force for the kind of work that is likely to be required.” It predicts that “by 2025, digital technologies will create at least 12 million more jobs than they eliminate, as people with the right skills will be needed to program, maintain, and repair them.”
High schools, training centers, apprenticeship programs, and in-work retraining, or rotational programs all contribute to the process of nurturing talent with the right mix of technical, applied, and human skills.
Education, community, and outreach
As U.S. schools and colleges extend teaching in automation, robotics, computing, and data analysis, this will mutually enrich both STEM students and the manufacturing sector. And businesses can help themselves by reaching out to the education sector and also their local community—the more so now that they’re bringing manufacturing back home.
A 2021 Deloitte study into “creating pathways for tomorrow’s workforce today” notes that businesses benefit when, for instance, they:
- engage directly with students, introducing them to the huge potential offered by smart manufacturing and asking them what they expect to value in a manufacturing role;
- foster strong links with the local community, both to attract people to entry-level roles and to help current workers feel more connected to home life; and
- embrace the principles of diversity, equity, and inclusivity (DEI) in order to broaden their company’s culture and increase the chances of attracting top talent.
Advanced learning
Whilst it is said that the best time to learn a new skill is right when you need it, learning on the job isn’t always practical or safe. In addition, manufacturers who invest in smart manufacturing technologies without properly understanding the skills required to run, manage, and maintain the new equipment or control system will suffer a longer time to value, as well as increased commissioning and support costs to external service providers while they recruit or retrain staff.
Manufacturers are investing in advanced training centers that give learners access to a full range of the latest technology. One such company is ABB Robotics, which has training centers around the world, including the U.S., as well as its own ABB University offering online and location-based courses.
There are many communities of interest who provide learning resources - webinars, whitepapers and industry insights on the pages of the A3 Association for Advancing Automation is a another great resource for upskilling on advanced manufacturing technology. They also have a podcast for the robot industry. Universal Robots also have an education center to help build the skills and experience future workers need to thrive in the smart manufacturing environment.
Increasingly, too, manufacturers are recreating or emulating the workplace in a digital twin: a virtual “mirror” of some or all of their operations. Digital twins—which already are a multi-billion-dollar industry that is set to grow—enable companies to run training centers for both STEM students and new or reallocated workers. Learners can safely trial processes—such as working with cobots—and they get the added benefit of seeing how manufacturers use twins to optimize workflows, predict and avert problems, and more. Virtual training is much faster than classroom learning, and builds confidence rapidly.
Apprenticeships, buddy programs, job rotation
Apprenticeships and internships have long provided hands-on training and experience. Two of our own interns, Debbie and Vincent, gained hands-on experience in robot programming and machine-vision quality control respectively. As Debbie explains, “The highlight of my internship was that I got to work with a high level of technology and innovation, that I could apply what I learned at university, and the positive and inclusive work environment at Facteon.”
Similarly, buddy programs bring tech-savvy recruits into collaboration with seasoned workers, enabling each to learn off the other. You can also upskill your workforce, and nurture dynamic thinking, by implementing job rotation programs. At the same time, you may need to rethink traditional roles: are they too narrow? Do they stifle out-of-the-box thinking? Do they reward creativity? Do they permit designers to make mistakes and put their learnings to use?
Invest in your workforce
The manufacturing revolution unleashed by data-driven digital tech is also disrupting traditional modes of work. If you’re shifting over to a smart manufacturing model that requires a broad and agile skills ecosystem, the solution to filling roles won’t lie in a sit-back-and-wait strategy, but in investing in the capacity of your workforce as much as in the technology itself, so that they are with you on the journey, and so that you enable workers to exploit their human skills—innovation, decision-making, adaptability—where they create the most value.
This is where we can help: by implementing smart solutions that are tailored to your operation, and working with you to find and build a skilled labor pipeline.
Find out more
Speak with one of our consultants to find out how your business can benefit from smart manufacturing solutions. Contact Facteon via our contact page.
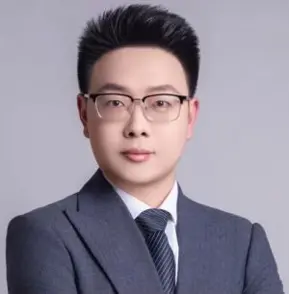
Victor Ding
Victor has more than 12 years of management experience in diverse fields, benefiting from his educational background in different periods, which has created his rich management ability. The engineering machinery background has given him a rigorous and logical technical foundation combined with a better understanding of the essence of manufacturing, and the MBA education has infused Victor's management with a systematic approach. His global work experience opened up his international perspective.
Victor has made remarkable achievements in strategic management and operations, as well as marketing and sales of multinational enterprises. As a Director and Vice GM of the company, he is committed to strengthening the cooperation between China and New Zealand and injecting strong impetus into the high-quality development of the Group.